Walk-in freezers and coolers are among the most heavy-duty and costly assets in any restaurant. A sudden failure can derail your entire kitchen operation, leading to spoiled inventory, lost revenue, and expensive emergency repairs. By prioritizing regular walk-in freezer maintenance, you can prevent these disruptions and save thousands of dollars in the long term.
Why Regular Maintenance Matters
- Prevents Unexpected Breakdowns: Routine checkups help identify minor issues before they become major repair bills.
- Protects Food Quality: Consistent temperatures ensure your ingredients and meals remain fresh and safe.
- Reduces Energy Bills: Well-maintained refrigeration units run more efficiently, cutting down on monthly utility costs.
- Extends Equipment Lifespan: Proper care adds years to your walk-in freezer’s service life, reducing the need for frequent replacements.
A Guide to Cost-Effective Upkeep
In this blog series, we’ll show you practical steps and expert tips to keep your walk-in cooler or freezer in prime condition. Following these guidelines not only boosts operational efficiency but also safeguards your bottom line. From cleaning and temperature checks to professional inspections, each step can make a significant difference in your annual expenses.
Save Thousands with Expert Walk-In Freezer Maintenance
Keep your commercial refrigeration running smoothly and your budget intact. Hood Builder offers reliable service and preventative care for restaurants and commercial kitchens of all sizes.
Call us at 303-777-7720 or Get a Free Quote today!
The Importance of Regular Maintenance for Walk-In Freezers
Walk-in freezers and coolers come in a variety of sizes and models, each tailored to optimize performance and energy consumption in a restaurant setting. Because these systems are so critical to your day-to-day operations—storing perishable goods and maintaining food safety—proactive maintenance isn’t just recommended; it’s essential.
Why Proactive Maintenance Is Non-Negotiable
- Prevent Costly Breakdowns
Routine inspections and timely repairs can stop small issues from becoming major equipment failures. - Maintain Food Quality
Consistent, properly regulated temperatures preserve food freshness and safety, reducing waste and health risks. - Enhance Energy Efficiency
Well-serviced units run more efficiently, helping you lower utility costs and meet sustainability goals. - Extend Equipment Lifespan
Regular maintenance prolongs the life of your walk-in cooler or freezer, delaying expensive replacements and upgrades.
Essential Design Considerations
Before focusing on maintenance and repair, ensure your walk-in freezer or cooler is properly designed and equipped:
- Emergency Features
- Alarms: Alert your staff to temperature fluctuations or door left ajar.
- Exit Door & Safety Release Mechanism: Prevent entrapment and ensure safe evacuation.
- Emergency Lighting & Ceiling Plugs: Offer visibility during power outages or critical situations.
- Operational Protocols
- Staff Usage Guidelines: Keep a clear, accessible protocol on loading, unloading, and handling procedures.
- Temperature Monitoring: Maintain easy-to-read temperature gauges or digital controllers for real-time tracking.
- Documentation & Records
- Maintenance Log: Track inspections, repairs, and parts replacements for ongoing accountability.
- Safety & Emergency Protocols: Ensure all documentation is well-organized and readily available.
By implementing these design and safety features upfront, you lay the groundwork for smooth operations and full compliance with health and safety standards. In the following sections, we’ll explore detailed maintenance tips and key repair insights to help you get the most from your walk-in freezer or cooler.
Top Indicators Your Walk-In Freezer Needs Professional Repairs
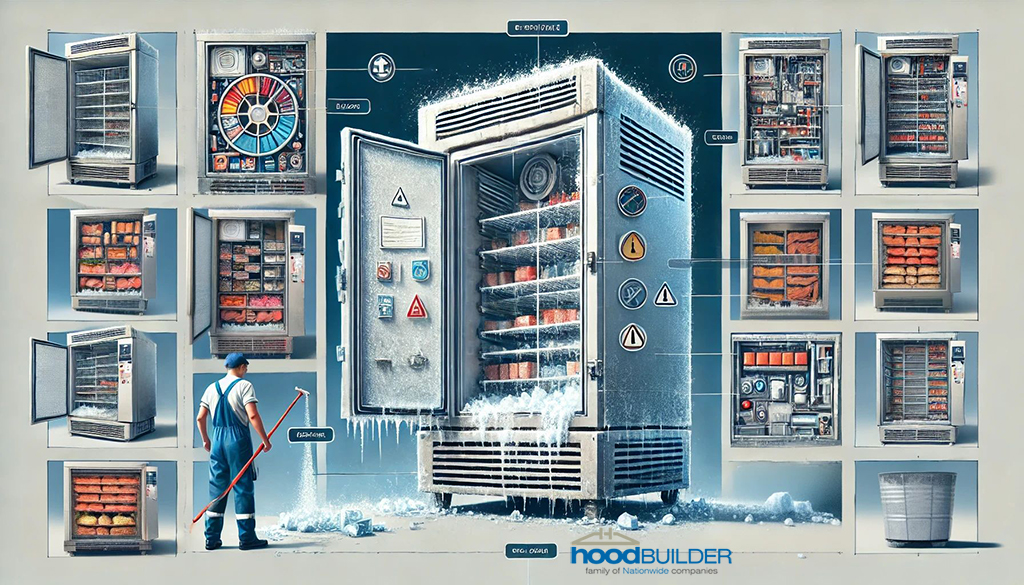
Even the most robust commercial refrigeration units aren’t immune to wear and tear. Whether due to poor maintenance, age, or mechanical failures, walk-in freezers and coolers may show signs of trouble that call for immediate professional attention. Below are the most common red flags to watch out for:
1. Unstable Temperature
- Why It Matters: Maintaining a consistent temperature is crucial for food quality and safety.
- What to Watch For: If the thermostat shows frequent spikes or dips, or if you notice your inventory spoiling faster than usual, it’s time for an inspection.
2. Strange or Loud Noises
- Why It Matters: Unusual sounds can indicate mechanical stress, component damage, or debris buildup.
- What to Watch For: Humming, clanking, or grinding noises often signal a deeper issue—get a technician’s opinion before it worsens.
3. Persistent or Foul Odors
- Why It Matters: Off-smelling air inside the freezer usually points to improper temperature control or even leaks that foster bacterial growth.
- What to Watch For: If cleaning doesn’t resolve the odor, contact a commercial freezer repair specialist to find the root cause.
4. Power Fluctuations
- Why It Matters: Frequent power cycling strains the motor and increases the risk of a complete breakdown.
- What to Watch For: If the unit repeatedly switches on and off or struggles to start, schedule a service call to prevent more costly damage.
5. Excessive Frost or Ice Buildup
- Why It Matters: A thin layer of frost is normal in certain models, but heavy ice accumulation stresses the freezer’s components and drives up energy usage.
- What to Watch For: Frost that quickly reappears after manual defrosting or blocks vents and doors is a clear signal of underlying issues.
When you spot any of these warning signs, don’t wait. Proactive repairs can save you from expensive downtime, product loss, and skyrocketing utility bills. If you suspect trouble, reach out to a trusted commercial refrigeration service provider to keep your walk-in freezer running optimally.
Best Practices for Walk-In Cooler and Freezer Care
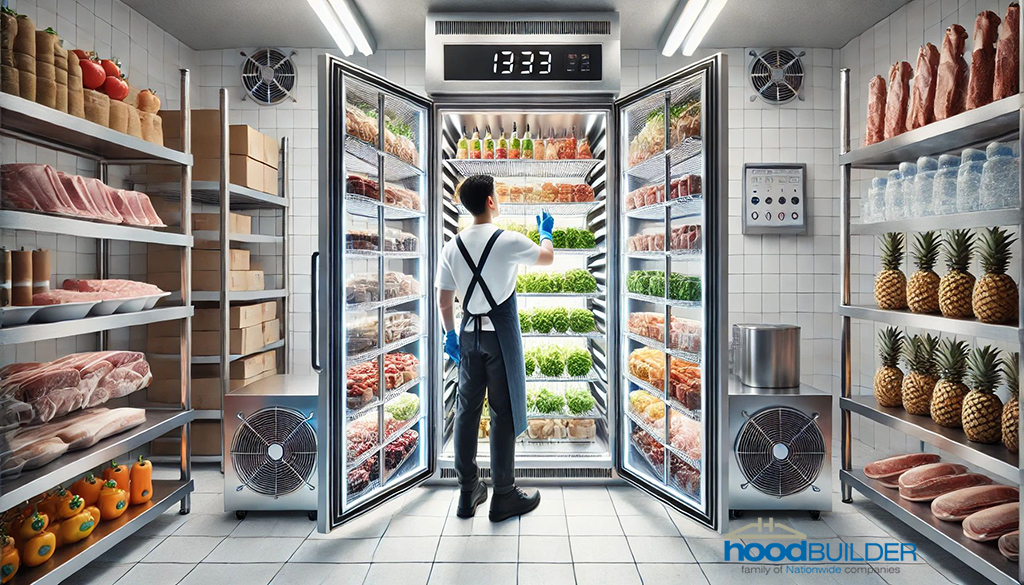
A well-maintained walk-in cooler or freezer is crucial for food safety, energy efficiency, and long-term cost savings. Below is a practical checklist you can share with your team to help ensure peak performance and extend the life of your refrigeration equipment:
- Daily Temperature Checks
- Record internal temperatures at least once per day to catch fluctuations early.
- Door Seals & Gaskets
- Inspect for wear or damage; replace any torn or cracked gaskets to maintain a proper seal.
- Regular Cleaning & Sanitization
- Wipe down interior surfaces to prevent bacterial growth and unpleasant odors.
- Proper Airflow & Stocking
- Avoid overloading shelves, ensuring cold air can circulate freely.
- Evaporator Coil Maintenance
- Keep coils clear of debris for efficient heat exchange.
- Monthly Condenser Coil Inspections
- Clean dirt, dust, or grease buildup that can force the system to work harder.
- Door Hinges & Closures
- Verify smooth operation; misaligned doors let cold air escape.
- Door Sweeps & Curtains
- Test and replace any faulty parts to reduce warm air infiltration.
- Leak Detection
- Fix water leaks promptly to prevent mold and damage to sensitive components.
- Unusual Noises or Vibrations
- Investigate odd sounds; they often indicate mechanical stress or failing parts.
- Insulation Panels
- Replace damaged or missing panels to maintain consistent temperatures.
- Drain Lines
- Ensure they’re clear of blockages to avoid standing water and ice buildup.
- Temperature Controls & Sensors
- Calibrate as needed for accurate readings.
- Regular Defrosting
- Prevent excessive ice buildup that strains the system and inflates energy costs.
- Fan & Motor Checks
- Confirm that all fans are spinning freely and motors aren’t overworked.
- Staff Training
- Teach proper loading techniques to optimize airflow and prevent product damage.
- Alarm & Monitoring System Tests
- Ensure that warning indicators function correctly for real-time problem detection.
- Scheduled Professional Inspections
- Partner with a commercial refrigeration expert for periodic tune-ups and repairs.
- Clean Surrounding Areas
- Keep the space around your unit clear of clutter to improve air circulation.
- Weatherstripping
- Use high-quality seals to block warm air from entering the unit.
For more official guidance, consult the latest Department of Energy recommendations on maintaining walk-in coolers and freezers.
Prevent Costly Downtime
Avoid sudden breakdowns and sky-high energy bills by following these best practices. For tailored installation, repairs, and preventative maintenance, contact Hood Builder—your trusted partner in commercial refrigeration solutions.
Talk to a Specialist today or call 303-777-7720 to keep your walk-in cooler or freezer operating at its best.
Frequently Asked Questions About Walk-In Freezer Maintenance
Below are common questions we receive about maintaining walk-in freezers and how proactive care can safeguard your food quality, energy efficiency, and operational budget.
1. Why Is Regular Maintenance Important for Walk-In Freezers?
Answer: Routine maintenance helps identify and address potential issues—such as failing parts, temperature fluctuations, or damaged seals—before they lead to costly breakdowns or food spoilage. By scheduling regular checkups, you extend your freezer’s lifespan and minimize emergency repair expenses.
2. How Can I Tell If My Walk-In Freezer Needs Repairs?
Answer: Look out for unusual odors, strange noises, and inconsistent temperatures. These warning signs suggest underlying problems that require professional attention to prevent further damage and inventory loss.
3. How Does Unstable Temperature Impact Stored Food Quality?
Answer: Temperature swings cause repeated thawing and refreezing, leading to loss of flavor, texture degradation, and even spoilage. Maintaining consistent temperatures ensures your products remain fresh, safe, and compliant with health regulations.
4. What Should I Do If I Notice Strange Noises Coming from My Walk-In Freezer?
Answer: First, ensure the door seals are intact and the unit isn’t overloaded. If the noise persists, contact a commercial refrigeration specialist to diagnose and fix the problem before it results in a larger, costlier malfunction.
5. How Often Should I Clean and Sanitize the Interior Surfaces?
Answer: The frequency varies based on your model and usage volume. However, most facilities benefit from weekly cleanings and monthly deep sanitizations. Regular cleaning helps prevent bacterial growth, foul odors, and residue buildup.
6. Why Is It Important to Inspect Door Seals and Gaskets?
Answer: Doors are critical for maintaining cold air containment. Worn or damaged seals allow warm air to infiltrate, forcing the freezer to work harder and increasing energy costs. Regular inspections help you keep operational expenses in check.
7. Why Is Airflow Critical in Walk-In Freezers?
Answer: Proper airflow ensures consistent cooling, preventing moisture and mold from accumulating. It also helps maintain even temperatures, reducing the risk of hot spots that can lead to spoilage or uneven freezing.
8. How Does Proactive Maintenance Save Money in the Long Run?
Answer: Small actions—like cleaning coils, checking door seals, and calibrating temperature sensors—can prevent major equipment breakdowns. By addressing minor issues early, you avoid emergency repair fees, reduce downtime, and protect valuable inventory.
9. How Can Professional Inspections Reduce Repair Costs?
Answer: Certified technicians have the expertise and specialized tools to pinpoint hidden issues and perform precise fixes. Their proactive approach often identifies problems in early stages, cutting down on expensive part replacements and extended downtime.
10. Can Proper Maintenance Reduce Energy Consumption for Walk-In Freezers?
Answer: Absolutely. A well-maintained system runs more efficiently, using less power to maintain optimal temperatures. Simple steps—like cleaning condenser coils and replacing worn gaskets—can lead to significant long-term energy savings.
Conclusion
Walk-in freezers and coolers are the backbone of restaurant operations, ensuring food stays fresh and inventory remains safe. When these systems fail—especially in high-volume kitchens—downtime can be both costly and stressful. By integrating routine inspections, following best practices, and acting on early warning signs, you can extend the life of your equipment, minimize repair costs, and maintain seamless kitchen operations.
Protect Your Investment and Keep Operations Running Smoothly
Hood Builder specializes in walk-in freezer maintenance and commercial refrigeration solutions that help restaurants reduce breakdowns and cut energy expenses.
- Call (303) 777-7720 to speak with our experts.
- Or Contact Us for a free quote and discover how proactive care can save you time, money, and headaches in the long run.